Steel Building Prices: 2025 Cost Analysis & Buying Guide
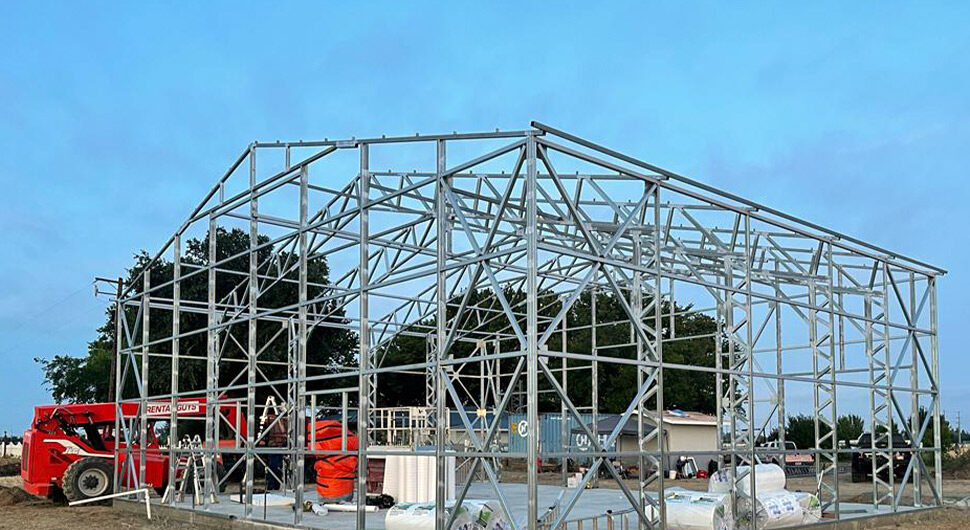
Thinking about investing in a steel building in 2025? Whether you’re planning a warehouse, a workshop, or even a residential structure, it is important to understand steel building costs. Prices fluctuate due to factors like material costs, labor, location, and design complexity.
But don’t worry—this guide will walk you through everything you need to know about steel building costs in 2025 and how to make a cost-effective investment.
Steel Building Price Overview in 2025
Steel building costs in 2025 vary based on size, complexity, and location. Below is a more detailed breakdown of cost expectations:
- Prefabricated steel building kits: Typically range from $15 to $25 per square foot, depending on design specifications and materials used.
- Fully installed structures: Generally, they cost between $24 to $43 per square foot, factoring in labor, site preparation, and customization options.
- Industrial-grade steel buildings: More complex structures with specialized reinforcements may range from $50 to $100 per square foot.
- Agricultural or storage buildings: Typically, on the lower end, around $10 to $20 per square foot due to simpler designs and minimal customization.
These figures are averages and may fluctuate due to global steel prices, economic conditions, and supply chain disruptions. To get an accurate estimate, it is advisable to compare quotes from multiple suppliers and factor in location-specific cost variations. Get your free quote from American Steel Carports today.
Factors Affecting Steel Building Prices
Steel building costs in 2025 are influenced by multiple factors. Hence, it makes sense to understand how each element contributes to the final price. Here are the primary factors that affect steel building prices:
1. Global Steel Market and Raw Material Costs
The price of steel fluctuates based on international supply and demand. Some of the influences include:
- Geopolitical factors such as trade tariffs and import restrictions.
- Raw material availability, including iron ore and recycled steel.
- Economic trends like inflation and construction booms that drive demand.
2. Geographic Location and Climate Considerations
Your location significantly impacts costs due to:
- Regional labor rates which vary up to 60% between different states.
- Shipping and delivery expenses—distance from steel mills and distribution centers matters.
- Climate factors that necessitate structural reinforcements, such as hurricane resistance in coastal areas or snow loads in colder regions.
3. Building Design, Size and Complexity
The complexity of your steel building directly influences cost:
- Larger buildings typically have lower costs per square foot due to economies of scale.
- Simple designs (rectangular, single-slope) are cheaper than multi-span or irregular structures.
- Customization—adding mezzanines, skylights, or specialized wall panels increases both material and labor costs.
4. Permits, Site Preparation and Foundation Costs
- Building permits vary by municipality and can range from $550 to $2,000.
- Site preparation, such as clearing, grading, and utility connections, add to overall expenses.
- Foundation types (slab, pier, or crawlspace) affect costs—slab foundations average $4 to $8 per square foot.
5. Installation and Labor Costs
Labor is a significant portion of steel building expenses:
- Hiring local contractors may reduce transportation and accommodation costs.
- Pre-engineered metal buildings (PEMBs) speed up assembly and lower labor costs.
- DIY construction for smaller buildings can save thousands but requires experience.
Understanding these cost factors allows buyers to make informed decisions and explore strategies to minimize expenses while ensuring a high-quality steel building investment.
Cost Breakdown of a Steel Building Project
Cost Component | Estimated Cost per Sq. Ft. |
Steel Building Kit | $15 – $25 |
Labor and Installation | $5 – $15 |
Foundation | $4 – $8 |
Insulation | $1.50 – $3 |
Doors and Windows | Varies based on customization |
Permits and Fees | $550 – $2,000 (one-time) |
How to Reduce Steel Building Costs in 2025
Reducing the cost of your steel building project requires strategic planning and informed decision-making. Here are some expert-recommended strategies to help you maximize savings:
- Choose standard sizes – Opt for common dimensions such as 30×40 or 40×60, which often result in lower manufacturing and material costs compared to custom sizes.
- Opt for Pre-Engineered Metal Buildings (PEMBs) – Pre-engineered buildings reduce construction time and labor costs due to their factory-fabricated components.
- Buy in the off-season – Steel prices and labor costs may be lower during off-peak months, allowing for potential savings.
- Limit custom features – Avoid unnecessary architectural complexities, such as intricate roof styles or excessive window and door openings, which increase both material and labor costs.
- Compare multiple quotes – Obtain at least three quotes from reputable suppliers to ensure you’re getting the best deal. You can get your free quote from American Steel Carports here.
- Consider DIY assembly – For smaller projects, assembling the steel building yourself can save thousands in labor expenses, provided you have the necessary skills and tools.
- Negotiate with suppliers – Many suppliers offer discounts for bulk orders or flexible delivery dates, so don’t hesitate to negotiate pricing.
- Use local contractors – Hiring experienced local contractors can minimize transportation costs and expedite the permitting process due to their familiarity with regional regulations.
- ·Explore financing options – Some manufacturers offer financing plans, allowing you to spread the cost over time and avoid large upfront expenses.
- Invest in energy-efficient features – Although this may involve a higher initial investment, energy-efficient insulation, and roofing materials can lower long-term operational costs and provide savings on heating and cooling.
Steel Buildings vs. Traditional Construction
Factor | Steel Buildings | Traditional Buildings |
Cost per Sq. Ft. | $15 – $43 | $100 – $200 |
Construction Time | 6 – 12 weeks | 4 – 12 months |
Lifespan | 50+ years | 30 – 40 years |
Maintenance | Low | High |
Energy Efficiency | High (with insulation) | Moderate |
Customization | Moderate | High |
Future Trends in Steel Building Costs
The steel building industry is evolving rapidly, with several key trends expected to shape costs in 2025 and beyond:
- Sustainability and green steel – Eco-friendly production methods, such as hydrogen-based steel manufacturing and increased recycling, are gaining traction. While initial costs may be higher, these methods could help stabilize long-term pricing and align with stricter environmental regulations.
- Automation and AI in fabrication – Robotics and artificial intelligence are revolutionizing the steel industry by enhancing precision, reducing waste, and lowering labor costs. As adoption increases, efficiency improvements could make steel buildings more cost-effective.
- Modular and hybrid construction – The rise of modular building techniques allows for faster assembly and potential cost savings. Hybrid construction methods, integrating steel with materials like concrete or wood, may further optimize expenses while maintaining structural integrity.
- Smart technology integration – Smart sensors embedded in steel structures will enable real-time monitoring of building health, reducing maintenance costs and improving safety. Predictive analytics will help detect structural issues before they become costly problems.
- Geopolitical and supply chain considerations – Global trade policies, tariffs, and supply chain disruptions will continue to impact steel pricing. Diversification of suppliers and domestic steel production initiatives may help mitigate price volatility.
- Energy efficiency and insulation advances – Improvements in insulation materials and energy-efficient coatings will enhance the thermal performance of steel buildings, leading to long-term savings in operational costs.
- Customization and prefabrication growth – As demand for highly customized yet cost-efficient solutions grows, pre-engineered steel buildings will become even more popular. Advances in prefabrication technology will allow for greater customization without significantly increasing costs.
Is a steel building a smart investment in 2025?
With rising material costs and evolving construction trends, steel buildings remain a cost-effective and durable option compared to traditional structures. While initial prices range between $15 and $43 per square foot, careful planning, supplier comparison, and strategic purchasing can ensure you get the best deal.
If you’re considering a steel building in 2025, now is the time to start planning. By staying informed and proactive, you can lock in a great price and secure a long-lasting, cost-efficient building solution. Get your free quote from American Steel Carports today. Or explore our collection here.